Introduction to OEE monitoring in manufacturing
OEE monitoring is a method used to track and measure the performance of manufacturing equipment in order to identify areas for improvement and optimize production efficiency.
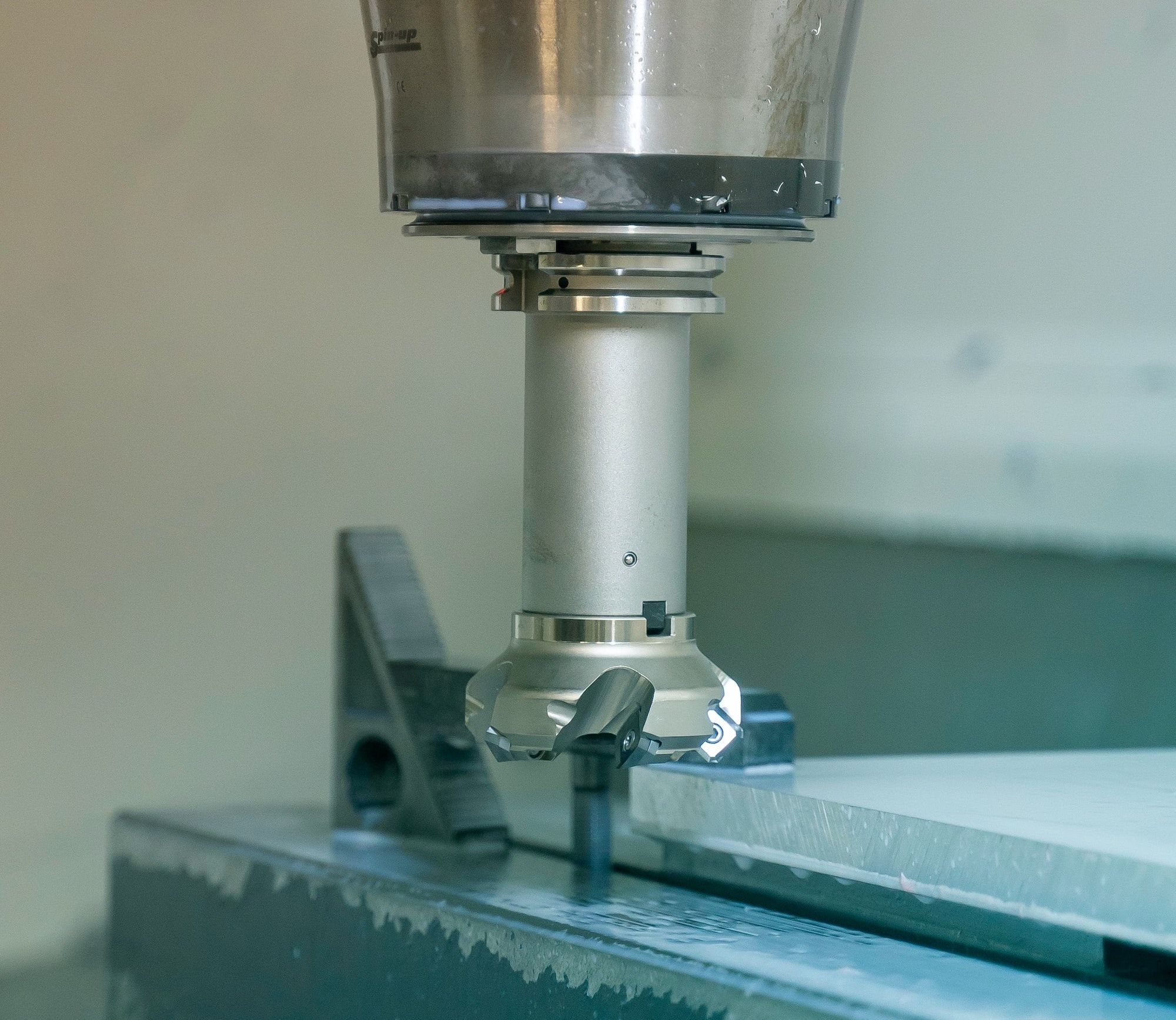
In the highly competitive manufacturing industry, maximizing production efficiency is critical to success. This is where Overall Equipment Effectiveness (OEE) monitoring comes in. OEE monitoring is a method used to track and measure the performance of manufacturing equipment in order to identify areas for improvement and optimize production efficiency.
What is OEE monitoring?
OEE monitoring is a process used to measure the performance of manufacturing equipment in terms of three key factors: availability, performance, and quality. By tracking these factors and analyzing the data, manufacturers can identify areas for improvement and optimize their production processes to increase efficiency and profitability.
Availability: Availability measures the percentage of time that equipment is available for production. This includes both planned downtime (e.g. maintenance, tool changes) and unplanned downtime (e.g. breakdowns, material shortages).
Performance: Performance measures the rate at which equipment produces parts or products in comparison to its maximum capacity. This includes factors such as speed losses, minor stops, and idling.
Quality: Quality measures the percentage of products that are produced to the required standard, without defects or rework.
To calculate OEE, these three factors are multiplied together to give a single score. An OEE score of 100% indicates that the equipment is operating at maximum efficiency, while a score below 100% indicates room for improvement.
Why is OEE monitoring important?
OEE monitoring is important because it provides a clear picture of the performance of manufacturing equipment, allowing manufacturers to identify areas for improvement and optimize their processes. By optimizing processes, manufacturers can reduce downtime, increase throughput, improve quality, and reduce costs. This, in turn, leads to increased profitability and competitiveness.
Benefits of OEE monitoring
There are several benefits to implementing OEE monitoring in manufacturing processes, including:
- Improved equipment utilization: By identifying areas of downtime and inefficiency, manufacturers can optimize their equipment utilization and reduce waste.
- Increased throughput: By improving the performance of equipment, manufacturers can increase throughput and produce more products in less time.
- Improved quality: By identifying and addressing quality issues, manufacturers can improve product quality and reduce the need for rework.
- Reduced costs: By reducing downtime, improving efficiency, and optimizing processes, manufacturers can reduce costs and increase profitability.
Read more about OEE benefits in the blog "5 benefits of OEE monitoring for manufacturers".
Implementing OEE monitoring
To implement OEE monitoring in manufacturing, there are several steps that must be taken:
- Define the scope: Determine which equipment will be monitored and what data will be collected.
- Select metrics: Identify the metrics that will be used to calculate OEE, such as availability, performance, and quality.
- Collect data: Collect data on equipment performance using sensors, manual data entry, or other methods.
- Analyze data: Analyze the data to identify areas for improvement and optimize processes.
- Take action: Take action to address identified issues and optimize processes to improve efficiency and profitability.
Learn more about the various OEE technologies in "Top OEE monitoring tools for manufacturing"
Conclusion
Overall Equipment Effectiveness (OEE) monitoring is a valuable tool for manufacturers seeking to optimize their production processes and increase efficiency. By tracking availability, performance, and quality, manufacturers can identify areas for improvement and take action to optimize processes, reduce downtime, increase throughput, improve quality, and reduce costs. Ultimately, implementing OEE monitoring can lead to increased profitability and competitiveness in the manufacturing industry.