Manufacturing Excellence with MES and IoT: The Future of Operations with IoTFlows SenseAi
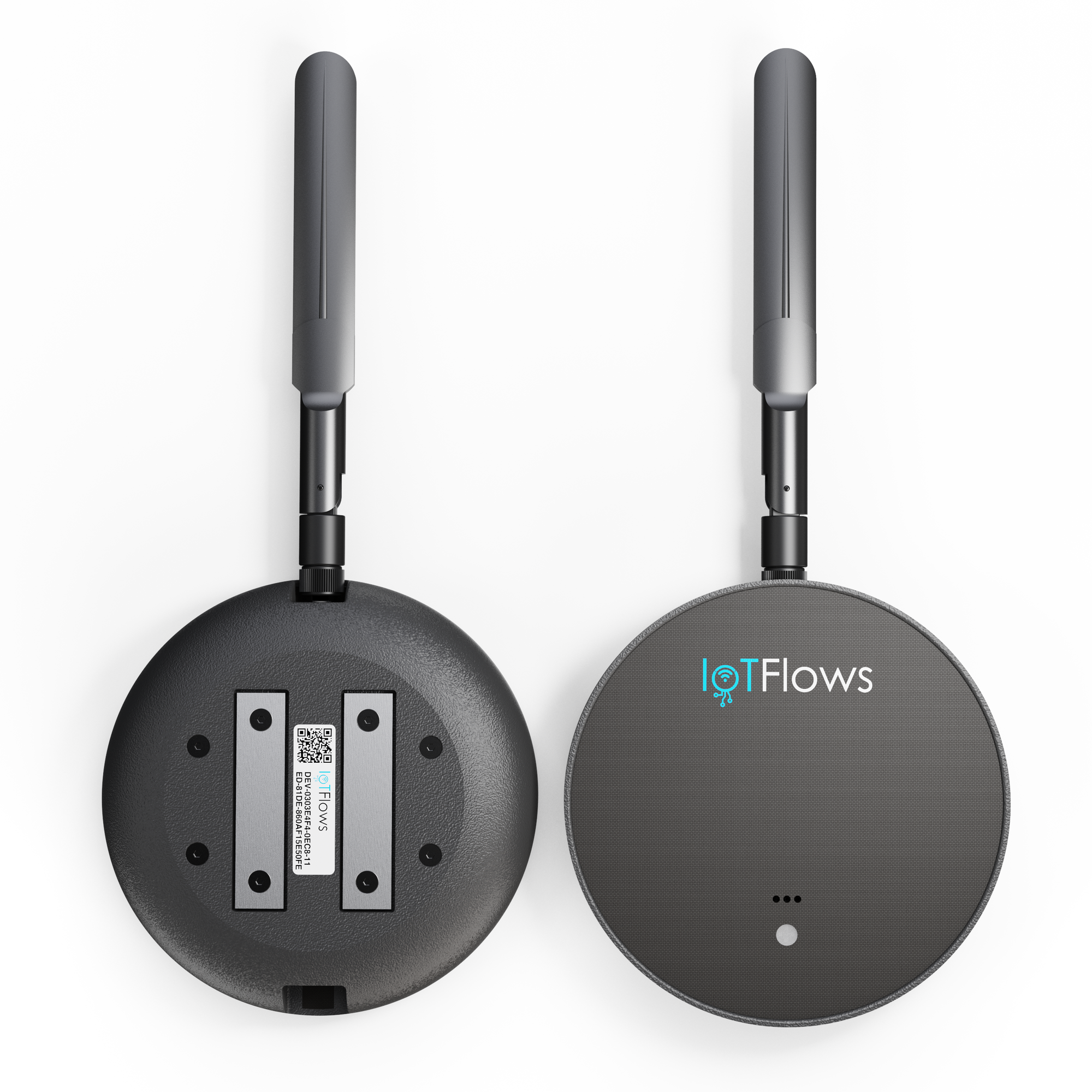
What is MES and How IoT is Changing the Game?
Manufacturing Execution Systems (MES) are critical in today's industrial landscape, serving as the backbone for optimizing manufacturing throughput. MES bridges the gap between the planning of production and the actual production process by tracking and documenting the transformation of raw materials to finished goods. But as technology evolves, so too does the role of MES, particularly with the advent of the Internet of Things (IoT).
IoT is redefining the way we manage and optimize manufacturing operations. By connecting machines, sensors, and systems, IoT enables real-time data collection, analysis, and insights that drive better decision-making and enhanced operational efficiency. The combination of MES and IoT is creating smarter factories where everything is interconnected and optimized for peak performance.
The Importance of MES in Optimizing Manufacturing Throughput
To truly optimize manufacturing throughput, you must first measure the key metrics that directly impact your operations. One of the most critical metrics in this regard is Overall Equipment Effectiveness (OEE). OEE provides a comprehensive view of how effectively your manufacturing process is being utilized. It considers factors such as machine availability, performance, and quality to give you a clear picture of your production efficiency.
Measuring machine utilization is vital in understanding how well your resources are being used. Accurate measurement of machine utilization not only helps in optimizing production but also in identifying areas of improvement that can lead to significant cost savings and increased output.
The Benefits of Measuring Machine Utilization Automatically
Traditionally, machine utilization has been measured manually, a process that is time-consuming, prone to errors, and often incomplete. Modern technology, however, offers automated solutions that provide accurate, real-time data without the need for human intervention. These automated systems can capture utilization data continuously, ensuring that nothing is missed and that the data is as accurate as possible.
Automated measurement of machine utilization brings several advantages:
- Accuracy: Eliminates human error, providing precise data.
- Efficiency: Saves time and resources by automating data collection.
- Comprehensiveness: Ensures all relevant data is captured for thorough analysis.
- Real-time Monitoring: Provides immediate insights, allowing for prompt action when issues arise.
Modern Ways to Measure Machine Utilization: Pros and Cons
There are various modern methods to measure machine utilization, each with its pros and cons:
Machine Data Protocols (e.g., MTConnect):
- Pros: Direct data from the machine, detailed insights, integration with existing MES.
- Cons: Not universally available, accuracy issues, can be tricked by non-productive operations (e.g., running the spindle without cutting).
Sensor-Based Monitoring:
- Pros: Can be installed on any machine, regardless of age or protocol; accurate real-time data.
- Cons: Requires sophisticated algorithms for data interpretation.
The Importance of Capturing Utilization Data from All Machines
To truly optimize your operations, capturing utilization data from all machines in a plant is crucial. Focusing on just one or a few machines can provide an incomplete picture, leading to suboptimal decisions. When you have data from all machines, you can see the bigger picture, identify bottlenecks, and ensure that every aspect of your production process is running smoothly.
The benefits of capturing utilization data from all machines include:
- Holistic View of Operations: Understand the performance of your entire production line.
- Identifying Bottlenecks: Pinpoint areas where inefficiencies are occurring.
- Improved Decision-Making: Make informed decisions based on comprehensive data.
- Enhanced Productivity: Optimize the use of all resources for maximum output.
The Challenge of Data Acquisition from Legacy Machines
Not all machines are equipped for easy data acquisition. Many legacy machines lack the necessary controllers, speak in proprietary protocols, or simply don’t have a standard way to extract data. This presents a significant challenge for manufacturers looking to implement a modern MES.
While protocols like MTConnect are promising, they are not universally supported, and even when available, they can sometimes provide inaccurate data. For example, MTConnect and similar protocols may report runtime and part counts, but they can be tricked by operations that are not truly productive, such as reducing the feed rate or running the spindle without cutting.
IoTFlows SenseAi: A Game-Changer in Utilization Monitoring
In contrast, physical principles like machine vibration offer a reliable method for utilization monitoring. IoTFlows SenseAi leverages advanced pattern recognition algorithms to analyze machine vibrations and acoustics, providing accurate insights into machine utilization, part production, machine health, and more.
With SenseAi, you can monitor any industrial equipment, regardless of its age or communication protocol. The plug-and-play nature of SenseAi makes it easy to adopt across all your machines, providing you with a unified dashboard that offers real-time and historical reports on OEE, machine health, downtime reasons, and much more.
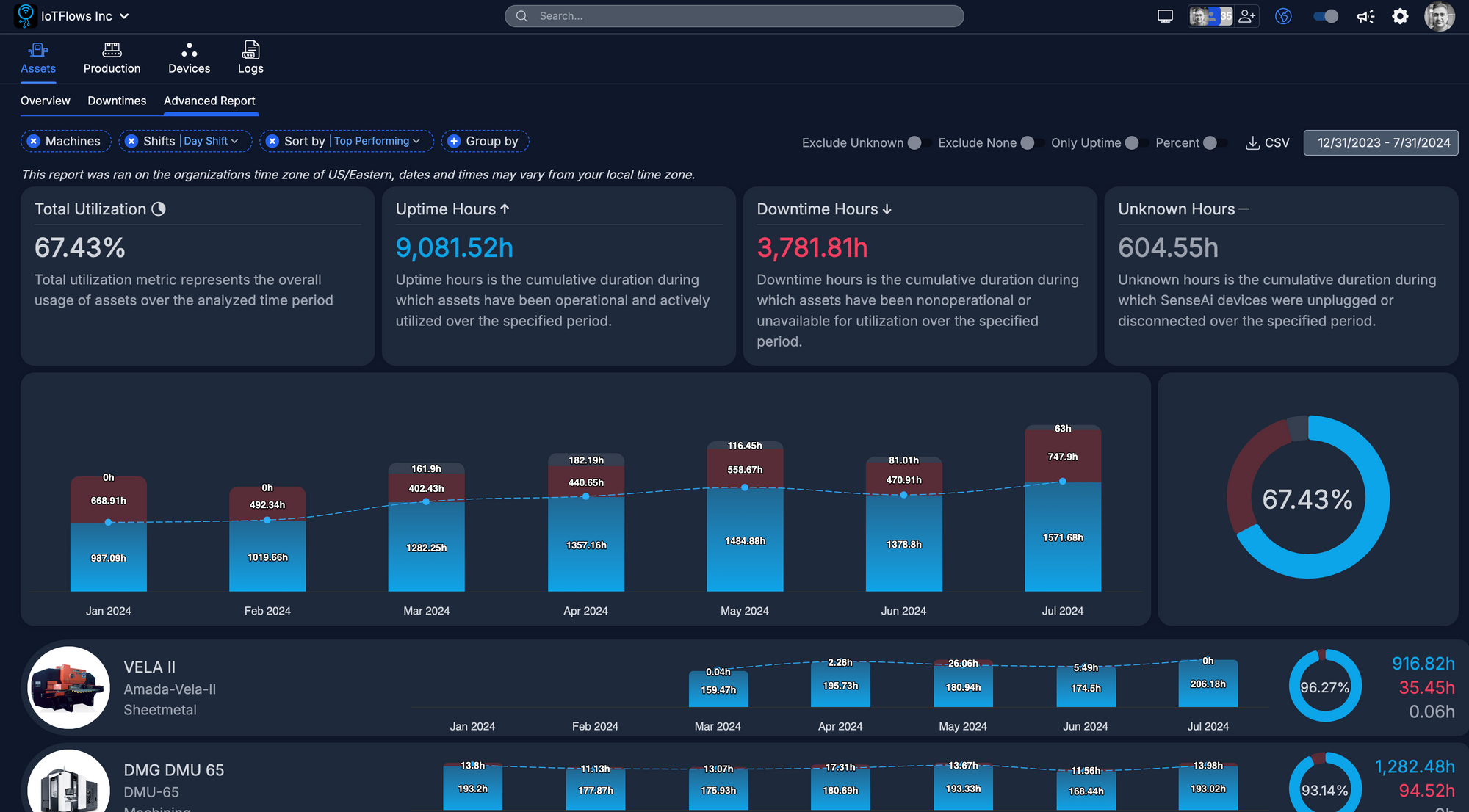
Why Choose SenseAi for Your Manufacturing Operations?
SenseAi by IoTFlows is not just a tool; it’s a comprehensive solution that accelerates your journey toward digital transformation. By installing SenseAi, you eliminate the need to open machine controllers, run cables, or worry about network configuration and security. It’s a hassle-free solution that delivers unparalleled value, helping you onboard all your machines into a connected ecosystem.
With SenseAi, you gain:
- Comprehensive Machine Monitoring: Analyze all machines on one platform.
- Accurate and Reliable Data: Trustworthy insights based on physical principles.
- Ease of Installation: No need for invasive setups or complex configurations.
- Holistic Operational Insights: From utilization to machine health and beyond.
- Seamless Integration: A modern, scalable solution that fits any manufacturing environment.
Join the IoTFlows Family
SenseAi can be just the beginning of your partnership with IoTFlows. By joining the IoTFlows family, you’ll gain access to an ever-expanding suite of tools designed to enhance equipment monitoring, collaboration, project management, task managements, and more. All these features are integrated into a well-connected ecosystem that improves the overall operations of your company.
Ready to take your manufacturing operations to the next level? Book a demo today and see how SenseAi can transform your production line.