Industry 4.0, IoT, and Digital Twin: The Journey Towards a Smart Manufacturing Future
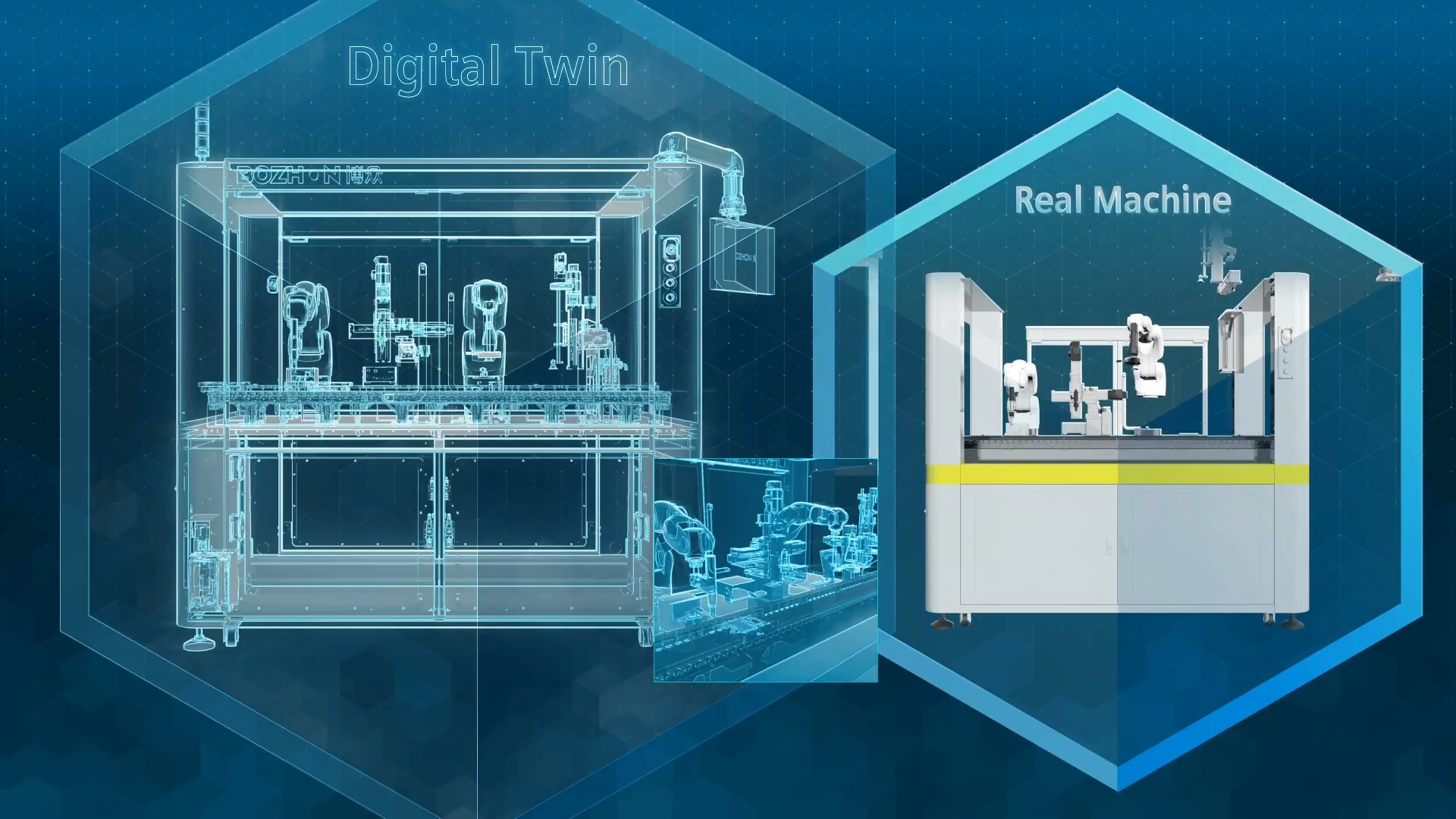
The fourth industrial revolution, commonly known as Industry 4.0, is transforming the manufacturing landscape with the integration of advanced technologies. At the heart of this revolution lies the Internet of Things (IoT) and the concept of digital twin, promising unprecedented improvements in efficiency, productivity, and cost-effectiveness. However, despite the significant progress made, the manufacturing industry still faces several hurdles in achieving the full potential of Industry 4.0. In this article, we will explore the meanings, benefits, and promises of Industry 4.0, IoT, and digital twin in manufacturing. Additionally, we will delve into the challenges faced in implementing these technologies and discuss potential solutions, including the notable IoTFlows SenseAi platform.
Understanding Industry 4.0, IoT, and Digital Twin:
- Industry 4.0: Revolutionizing Manufacturing: The concept of Industry 4.0 represents the integration of digital technologies into the manufacturing sector. It encompasses various principles such as connectivity, automation, data exchange, and real-time analytics. Industry 4.0 aims to create a smart factory environment that enables machines, systems, and humans to collaborate seamlessly.
- Internet of Things (IoT): The Internet of Things refers to a network of physical devices, vehicles, appliances, and other objects embedded with sensors, software, and connectivity capabilities. These devices collect and exchange data, enabling them to communicate and interact with each other without human intervention. In the context of Industry 4.0, IoT plays a crucial role in connecting machines, processes, and people, forming the backbone of a digitized manufacturing ecosystem.
- Digital Twin: A digital twin is a virtual replica of a physical asset, process, or system. It simulates the behavior, characteristics, and performance of its real-world counterpart in real-time. Digital twins enable manufacturers to monitor, analyze, and optimize their operations, predict maintenance needs, and simulate scenarios for process improvement and innovation.
Promises and Benefits of Industry 4.0, IoT, and Digital Twin in Manufacturing:
- Enhanced Operational Efficiency: One of the significant promises of Industry 4.0, IoT, and digital twin is improved operational efficiency. Real-time data collection, analysis, and predictive maintenance enable manufacturers to identify potential issues before they occur, minimizing downtime and optimizing equipment performance. You can read more about this and the benefits of monitoring equipment effectiveness in this article. Additionally, these technologies facilitate better resource allocation, supply chain management, and inventory control, leading to streamlined processes and reduced waste.
- Increased Productivity and Quality: Industry 4.0 technologies empower manufacturers to enhance productivity and product quality. By leveraging IoT sensors and connectivity, production processes can be optimized for increased speed, accuracy, and flexibility. Digital twins provide a virtual testing ground, allowing manufacturers to simulate and optimize production workflows, identify bottlenecks, and implement improvements. Quality control is also enhanced through real-time monitoring, defect detection, and data-driven decision-making.
- Cost Reduction and Sustainability: Industry 4.0, IoT, and digital twin have the potential to drive cost reduction and sustainability in manufacturing. By leveraging IoT and digital twin technologies, manufacturers can implement energy management systems, optimize resource utilization, and reduce waste. Lean manufacturing principles can be applied more effectively, ensuring just-in-time production and minimizing excess inventory. This not only leads to cost savings but also contributes to environmental sustainability and a reduced carbon footprint.
Challenges in Implementing Industry 4.0, IoT, and Digital Twin in Manufacturing:
Legacy Systems and Infrastructure: One of the significant challenges in adopting Industry 4.0 technologies is dealing with legacy systems and infrastructure. Many manufacturing plants still rely on outdated machinery and equipment that lack connectivity and compatibility with modern technologies. Integrating new technologies with existing systems requires careful planning, retrofitting, and investment.
- Data Management and Security: The vast amount of data generated by IoT devices and digital twins poses challenges in terms of data management and security. Manufacturing plants must establish robust data storage and processing capabilities to handle the volume, velocity, and variety of data. Moreover, ensuring data privacy, protection against cyber threats, and maintaining data integrity are critical concerns in an interconnected manufacturing environment.
- Workforce Adaptation and Skills Gap: Implementing Industry 4.0 technologies requires a skilled and adaptable workforce. Employees need to acquire new competencies, such as data analytics, cybersecurity, and digital literacy. However, there is a significant skills gap in the industry, and companies must invest in training and reskilling programs to equip their workforce with the necessary skills for the digital era. Furthermore, concerns about job displacement and the need for workforce buy-in present additional challenges.
Solutions and Approaches for Successful Implementation:
- IoT Platforms and Tools: A wide range of IoT platforms and tools are available to support the implementation of Industry 4.0 in manufacturing. These platforms offer features such as device management, data analytics, visualization, and integration capabilities. Popular examples include Amazon Web Services (AWS) IoT, Microsoft Azure IoT, and Siemens MindSphere. Choosing the right platform depends on factors such as scalability, compatibility with existing systems, and specific manufacturing requirements.
- Digital Twin Development: Creating digital twins requires specialized tools and software. These tools enable manufacturers to design, simulate, and monitor digital replicas of their physical assets and processes. Some notable digital twin platforms include Siemens' Simcenter, Dassault Systèmes' DELMIA, and PTC's ThingWorx. Integration with IoT data allows real-time monitoring and synchronization, providing valuable insights for optimization and decision-making.
- IoTFlows SenseAi, The Ultimate Industry 4.0 Solution: IoTFlows SenseAi is a comprehensive platform designed to address the challenges of implementing Industry 4.0, IoT, and digital twin in manufacturing by leveraging IoT and AI-powered machine performance monitoring solutions. It offers a range of features and benefits, including:
- End-to-end IoT connectivity and device management for seamless integration of sensors, machines, and systems.
- Advanced analytics and machine learning capabilities to derive actionable insights from real-time vibration, acoustics, and machine data.
- Digital twin modeling and simulation for virtual testing, optimization, and predictive maintenance.
- Robust security measures to protect data integrity and ensure compliance with industry standards.
- Scalability and flexibility to accommodate various manufacturing environments and specific business needs.
IoTFlows SenseAi has been successfully deployed in manufacturing plants across various industries, delivering tangible results in terms of operational efficiency, productivity gains, and cost reduction. Real-world examples of successful implementations demonstrate the platform's effectiveness in driving digital transformation and realizing the promises of Industry 4.0.
Conclusion:
While Industry 4.0, IoT, and digital twin hold tremendous potential for revolutionizing the manufacturing industry, there are still significant challenges to overcome. Legacy systems, data management, and workforce adaptation pose hurdles that need to be addressed to fully realize the promised benefits. However, with the right tools and solutions, such as the IoTFlows SenseAi platform, manufacturers can take significant strides toward achieving their Industry 4.0 goals. The future of smart manufacturing is within reach, and by embracing these transformative technologies, companies can drive innovation, competitiveness, and sustainable growth.
Industry 4.0, IoT, and digital twin have the potential to transform the manufacturing industry by enabling smarter, more efficient, and sustainable processes. While significant progress has been made, challenges remain, including legacy systems, data management, and workforce adaptation. However, with the right approach and solutions like IoTFlows SenseAi, manufacturers can overcome these challenges and unlock the full potential of Industry 4.0. The journey towards a smart manufacturing future is ongoing, and by embracing these technologies, companies can position themselves at the forefront of innovation and gain a competitive advantage in the ever-evolving global market.